Life Cycle Analysis
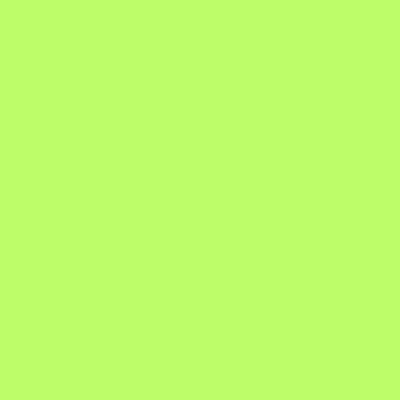
-
82% less greenhouse gas emissions
82% less greenhouse gas emissions
Our process is 100% electric and the electricity mix in France is low-carbon. Combined with our shorter recycling loop, the project’s carbon footprint is a lot smaller than the one of virgin production of styrene.
-
82% less impact on ecosystem quality
82% less impact on ecosystem quality
Our process emits less greenhouse gases and has a lesser impact on water scarcity. Our process does not require water or solvents.
-
73% less energy use
73% less energy use
Our process is a lot less energy-intensive than the production of virgin product because the recycling loop is shorter, i.e. we don’t need to go back as far down to the cracker step like traditional petrochemical processes do. In addition, our highly efficient technology produces the highest yield in the industry thanks to microwaves. Microwaves can be powered by renewable or low-carbon sources, as is the case in France.
-
94% less impact on water scarcity
94% less impact on water scarcity
We don’t use water or solvent in our process, thus preserving freshwater and our precious resources.
-
86% less impact on human health
86% less impact on human health
We don’t emit toxic emissions in the atmosphere, reducing the impact on human health issues such as respiratory diseases. In addition, the co-products of our process are recycled into other high-value applications.
Collaborating with the value chain
1 - The Pyrowave technology in itself only accounts for 12% of total emissions
The indicators described in the section above only consider this part of the value chain.
2 - 88% of environmental impacts stem from the value chain (scope 3), such as collection and sorting
3 - Sorting and Plastic waste collection counts for 38% of greenhouse gas emissions
Because longer transportation distances mean more greenhouse gases, waste should ideally be locally sourced. This is why Pyrowave’s modular solution adapts to local volumes and minimizes transportation.
Designing products for recycling and optimizing secondary sorting infrastructure is key for better quality feedstock leading to better sorting and minimizing sorting rejects.
4 - Incentives for recycled content
Mandatory recycled content targets are key to drive the recycling industry and create sustainable products. Prioritizing traceable content is a key element for consumer trust, which Pyrowave’s technology guarantees at 100%.
Want to learn more?
Want to check out our data, sources and assumptions?
For any questions regarding this LCA or for potential research collaboration,
please email info@pyrowave.com.
Methodology
System boundaries
The life cycle analysis (LCA) based on a scenario of an industrial project using the PYROWAVE technology was commissioned by PYROWAVE and modeled by the CIRAIG. It was peer reviewed by Quantis and a team of independent experts, including engineers. The data is sourced from EcoInvent 2020, the model used is the Impact+ methodology, all compliant with ISO 14040 and 14040 standards.
LCA based on a product and end of life approach
Such as recommended by the harmonization guide published by LCA consultancy Sphera1, we modeled our system boundaries to reflect the system expansion by addition approach. As the recycling process delivers multiple functions – both treating plastic waste and creating new materials – it shouldn’t only be compared to the virgin production creating new materials. As the figure above shows, we have expanded the system boundaries to add the process of plastic waste end-of-life to the reference scenario. This allows the multifunctional process of chemical recycling to be compared to the same functions delivered in the reference scenario. Thus, the services rendered by the two scenarios are the same: production of 1 kg of styrene monomer and 0.43 of co-products. This approach is entirely consistent with the universally recognized standard ISO 14044, under which our LCA study was conducted.
As such, the LCA compared:
- Pyrowave project scenario using catalytic microwave depolymerization of polystyrene (PS) waste
and - Reference scenario of virgin styrene production and end-of-life of PS waste (38% landfill and 62% incineration)
The results using this methodology (including scopes 1, 2, and 3) are available in the executive summary.
1 Christopher Koffler et al., ‘Life Cycle Assessment of Chemical Recycling: First Steps Towards Harmonization’ (Sphera, 2021), https://sphera.com/research/life-cycle-assessment-of-chemical-recycling/.
Here are results of Scopes 1 and 2: we isolated the styrene process from the rest of the value chain to highlight the impact of Pyrowave’s technology as the surrounding recycling value chain remains the same, no matter the chosen recycling technology.
The chosen system boundaries for Scopes 1 and 2, as illustrated above, correspond to the reception of purified incoming feedstock (from crude oil in reference scenario and sorted polystyrene waste in the Pyrowave scenario) and ends with the production of purified styrene monomer. The complete LCA document is accessible here.
- Energy sources. Data uses the French electricity grid for every step of the value chain, corresponding to 74% nuclear, 9% fossil fuels, 1% combustion renewables and 16% non-combustion renewables.
- Feedstock preparation. The purified feedstock input for the Pyrowave scenario arrives from a secondary sorting facility, where the post-consumer waste is assumed to reach a purity of nearly 95% polystyrene material.
- Styrene process. This step includes:
- reception of feedstock,
- extrusion-filtration separating the PS input from any remaining contamination,
- Catalytic Microwave Depolymerization (CDM), where polystyrene is broken down into various products including the monomer.
- The distillation that produces pure styrene monomer (99.8%) and co-products containing aromatics (cumene, ethylbenzene, and toluene) and oligomers,
- The incineration of direct process emissions (pyrolysis gas, char, extrusion rejects). We assume these by-products are incinerated with heat recovery.